|

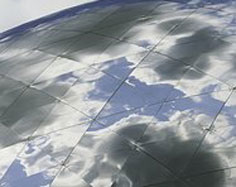
Written by Larry Tew
President and Co-founder
The Center for Error Management
Brighton, Colorado, 80602
www.ManageError.com
|
|
|
Summary
Due to the high percentage of the cost of
quality related to sales and a significant
percentage of errors attributed to humans,
the application of human error management
concepts and techniques can make significant
contributions in reducing the cost of quality
and improving an organization’s bottom
line. Error management activities can be correlated
to the three elements of the cost of quality
PAF model: prevention, appraisal, and failure.
Furthermore, proven successes in human error
management training evolving from the commercial
aviation industry’s crew resource management
are being adapted for a variety of industries.
This training provides techniques to identify
Mind Traps that can lead to error and introduces
Tools to detect and avoid errors, including
communication approaches to use the combined
knowledge and interaction of the entire team.
Organizations should consider the application
of error management concepts and techniques
as a valuable tool to reduce the cost of quality
and compliment ongoing activities such as
environmental safety and health, Lean, Six
Sigma, systems safety, and product assurance.
|
|
Introduction
Current research shows that the Cost of Quality
(COQ) can range anywhere from 15 to 40% of sales.
Even with the varying COQ ranges, there is no disagreement
that the cost of quality is very large and has significant
impacts to the bottom line profitability of an organization.
Edward Deming believed that the cost of non-conformance
(and the resulting loss of good will) was so high
that evaluating the cost of quality was unnecessary.
Phillip B. Crosby is frequently identified as the
individual who popularized the use of COQ in his
book Quality is Free. He referred to COQ as “the
price of conformance.” To meet basic objectives,
an organization must focus on increasing profits
by reducing the costs of quality through a variety
of methods, including the reduction of errors and
the elimination of non-value-added activities and
waste. In addition to the monetary costs of quality,
an organization must also consider the major impact
that poor quality can have on its current and future
customers and its market share.
Human error is a major contributor to non-conformances
and therefore COQ. Research shows that human error
is responsible for 35 to70% of accidents, incidents,
and non-conformances. This range generally holds
true in all industries. Error is generally defined
as a deviation from accuracy or completeness. More
specifically, the medical community defines an error
of execution as “the failure of a planned
action to be completed as intended” (Institute
of Medicine 2000). Crosby also acknowledged the
significance of human error when he stated, “Most
human error is caused by a lack of attention rather
than a lack of knowledge.”
In the mid-1970s, the National Aeronautics and Space
Administration (NASA), and subsequently the Federal
Aviation Administration (FAA), became significantly
involved in human error because of concern over
the increasing number of accidents. (Helmreich,
Merrit, Wilhelm 1999). They sponsored a study that
examined voice and data recorder information (black
boxes) obtained from aircraft accident scenes. The
study determined that cockpit crews were not performing
in the professional manner that their aircrew training
was expected to provide. The study concluded that
the human element in the cockpit was the initiating
factor in many of the accidents. Inappropriate decisions
and reactions to common flight conditions by pilots
in command actually created tragic accidents. In
addition to lack of effective leadership, another
major factor contributing to accidents was the lack
of assertiveness on the part of crew members who
knew that something was not right but did not feel
free to speak up. A reenactment of the crash of
Eastern’s Flight 401 into the Florida Everglades,
presented on the Public Broadcasting Service Nova
series program entitled “Why Planes Crash”,
paints a vivid picture of the disastrous affects
of lack of leadership and lack of assertiveness
on the part of the aircrew.
In response to the lack of performance by cockpit
teams, special training referred to as Cockpit Resource
Management was created. The cockpit training was
so successful in reducing accidents that the aviation
industry broadened the training to include flight
crew members and maintenance personnel, renaming
it Crew Resource Management (CRM). Since its initiation
in the 1970s, CRM training has become a part of
standard training for U.S. commercial, military,
and private aviation. It has been expanded to aviation
training throughout the world.
CRM focuses on training individuals and teams in
a number of error management areas. The training
provides techniques designed to identify the Mind
Traps affecting individuals and teams during daily
operations that can set them up for error. It also
provides them with Tools including communication
approaches to improve their combined knowledge and
interaction of the entire crew to detect and avoid
error opportunities. With assistance from the University
of Texas Department of Psychology, Aerospace Crew
Research Project, the research agency for the Federal
Aviation Administration, CRM has evolved into an
acceptance and recognition of human limitations
that can result in errors. The basic starting point
for managing human error is to understand and accept
Cicero’s statement in 200 BC that “To
err is human.” Although this statement suggests
that there is nothing we can do about errors, the
Pulitzer Prize winning author Pearl Buck said, “Every
great mistake has a half-way moment, a split second
when it can be recalled and perhaps remedied.”
Error management is based on the premises that we
can take advantage of this half-way moment. We can
learn to recognize when we are about to make a mistake
and we can be trained to manage human error by learning
to detect, avoid, mitigate, and preclude the recurrence
of errors. Due to the successes in aviation and
the recognition that human elements are the initiating
factor in almost every organizational accident,
incident, and error, a number of industries are
adapting the CRM training approach to their specific
needs.
|
Synergy
of COQ and Human Error Management
Based on the established high percentage of COQ
related to sales and the high percentage of errors
attributed to humans (35-70%), COQ and human error
are both areas of opportunity for the significant
improvement to an organization’s bottom line.
Developing a solution to reduce these percentages
requires examination of key elements of COQ and
human error management and how they can work together
to improve economic value.
Most quality cost models are based on a PAF
classification (Punkett and Dale 1987). The basic
categories of the PAF Model were identified by Armand
Feigenbaum (1956) and are described as: 1) Prevention—Refers
to those actions taken to ensure that a process
provides quality products and services, 2) Appraisal—Actions
that are designed to measure the levels of achieved
quality, 3) Failure—Actions
taken to correct quality in products or services
that are both internal (within the organization)
and external (after delivery to the customer).
The ultimate goal in reducing COQ is to eliminate
failure and to sustain a quality system through
continuous prevention efforts with minimal appraisal
activities. Human error management techniques use
the data from appraisal and failure activities to
assist in establishing and sustaining a preventive
culture. Again, since human error has been cited
as causing up to 70% of non-conformances, reducing
human error can have a major impact on reducing
failures that result in decreased COQ and major
improvements to the bottom line.
An example of Crew Resource Management training
being successfully applied in other industries is
the benchmark study by the Institute of Medicine
(2000) which showed between 44,000 to 98,000 deaths
occurred each year due to human error. The study
recommended that the medical industry adapt the
proven techniques of Crew Resource Management. Since
that time, fire departments have also recognized
the value of CRM and have created a major effort
to adapt these same techniques to the Fire Service.
Gary Briese, Executive Director of International
Association of Fire Chiefs, put the importance of
their efforts in perspective when he stated, “
In the 10 years it will take CRM to be introduced
nationally, we will attend 1,000 firefighter funerals…I
can’t get that out of my mind.”
Ongoing research at the Aerospace Research Project
continues to expand CRM through process improvement
efforts. They define error management as “using
all available data to understand the causes of errors
and taking appropriate actions, including changing
policy, procedures, and special training to reduce
their incidence of error and minimize the consequences
of those that do occur.” Clearly, the activities
associated with error management support organizational
efforts of prevention, appraisal, and reduction
in failures as a means to reduce COQ.
|
Methods
and Approaches
As shown by the date of Cicero’s statement,
human error has been around for a long time. However,
proven results of the application of error management
techniques show that with awareness of human Mind
Traps that cause errors and through the application
of error management Tools, human error can be detected,
avoided, mitigated, and precluded from recurrence.
In his book, Human Error, James Reason
noted that human psychology cannot be ignored. Error
management adaptations of CRM include addressing
a number of error management areas as shown in figure
1.
The number of management areas and training emphasis
in each area depends on the specific industry or
occupation being trained. For example, in law enforcement
the number one fatal error by police officers is
the Mind Trap of a risky attitude, (e.g. trying
to be a hero rather than understanding reality,
impulsivity). In training of police officers, emphasis
is placed on understanding Attitude Mind Traps and
the error management Risky Attitude Antidote Tools
(e.g. “It could happen to me”, “Taking
a chance is foolish”).
In his book Managing the Risks of Organizational
Accidents, James Reason created what he referred
to as the Swiss Cheese model which graphically displays
lines of defenses that an organization creates in
an attempt to engineer out the possibility of human
error. The Swiss Cheese Model has been adapted in
figure 2 to illustrate how the barriers of technical,
cultural, organizational, and the individual are
defenses against error. Identifying the individual
as “the last line of defense” has been
attributed to Dr. Edward Deming. Unfortunately,
as Reason points out, many of these barriers can
have holes like that of Swiss cheese allowing an
error opportunity to penetrate all the defenses
resulting in a loss. In addition, these defenses
are not static. Depending on specific circumstances
for each error opportunity they are changing all
the time. Error management provides Tools whereby
individuals and organizations can detect human Mind
Traps and fill the holes that lead to human error.
|
Figure 1 Error Management Areas,
The “Error Management Cube”
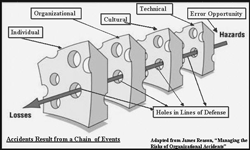
Figure 2 Adapted Swiss Cheese Model
|
An
explanation of the application of error management
techniques from the perspective of an individual or
last line of defense helps illustrate the error management
process. Phillip Crosby also stated that “Most
human error is caused by a lack of attention rather
than a lack of knowledge.” In the terminology
of CRM and error management, lack of attention is
identified as the Mind Trap “Loss of Situational
Awareness.” “Loss of Situational Awareness”
has been identified as the number one cause of human
error. This poses an interesting question. How do
individuals recognize that they have lost Situational
Awareness and how can they regain it? There are a
number of error management signs that can help an
individual identify that situational awareness (e.g.
distraction, fixation) has been lost as well as error
management Tools to help regain situational awareness.
One of the most powerful error management Tools that
humans have is the gut feeling that something is not
right which Malcolm Gladwell refers to as an “adaptive
unconscious” (Gladwell, 2005). This gut feeling
has been shown to be very effective in regaining situational
awareness.
Because of the differences in organizational structure,
culture, and technical processes, and the reality
that one training approach does not meet every organization
need, human error management must be adapted to
the unique characteristics and needs of each organization.
When discussing the application of CRM related training
to the Fire Service in the book Crew Resource
Management for the Fire Service (2004-2011), Randy
Okray and Thomas Lubnau II stated that, “It
is up to each department to decide what best fits
their local culture.” To be effective and
credible, the facilitator trainers should be thoroughly
familiar with all aspects of error management for
the specific industry they are training. This background
knowledge is necessary as they work with the organization
in the development of a case for intervention, conduct
of the initial training and implementation, sustaining
implementation, and evaluation of the effectiveness
of the error management program. Initial and sustaining
implementation activities should be supported through
the training of senior management and middle management.
In addition training is needed at the individual,
program, and team levels. Success in implementation
is assisted by
identification and training of program-unique error
management coaches. All these activities result in
an improved capability to break the chain of events
that can result in individual and group errors and
sustain the training as it becomes a part of the organization
culture and structure.
Expectations for reduction in errors, decrease
in cost of quality, and improvements to the bottom
line
After training, the implementation of basic techniques
and an organizational commitment to vigorously pursue
the reduction of errors, an error management culture
has been shown to mature into individual and group
activities, significantly decreasing COQ and improving
the bottom line. These activities include: 1) Focus
on detection of latent errors, 2) Conducting thorough
analysis of anomalies to determine systemic factors
leading to errors, and 3) Open sharing of resulting
information. Implementation has also resulted in important
by-products including: improved communication, team
building, and creation of an open atmosphere to speak
up when things do not seem right.
One error management technique being successfully
adapted in aviation, medicine, and aerospace is
that of anonymous reporting of near misses. The
application of error management techniques in an
aerospace company resulted in 43% reduction of accidents
in a two-year period. By instituting reporting and
detailed analysis of events and near misses, the
Norwegian Railroad (Chris Hart, undated) achieved
37% reduction in lost time and 40% reduction in
accidents. Another organization was recognized in
their incentive fee for their incorporation of error
reporting.
Error management should not be considered as a new
program but rather as an enhancement to existing
activities. One senior manager said, “I am
not giving you a new task you have plenty to do
already; but I am giving you techniques that will
help you be a better employee and leader.”
These techniques compliment and support ongoing
activities in a variety of activities including
risk management, environmental safety and health,
quality management, safety, CMMI, Lean Thinking
and Six-Sigma.
Error management related training and its implementation
has resulted in many positive comments and improvements
in organizational performance and effectiveness.
One program manager commented that “All the
team members now have a common knowledge core to
work with during a high stress time to detect the
possibility of an error.” After error management
training of a machine shop team, their anomaly reporting
system status was raised from “Yellow-Red”
to “Green. Another organization noted an increase
in reporting of near misses that might not have
been previously reported. They found that the information
obtained from reporting of near misses has led to
the identification and analysis of systemic conditions
that could lead to future accidents and incidents.
Conclusion
Because of the established high percentages of COQ
related to sales and the significant percentages
of errors attributed to human error, the application
of error management concepts and techniques can
make significant contributions to reducing the cost
of quality and improving an organization’s
bottom line. In their survey of models and best
practices, Schiffauerova, and Thomson confirm that
quality improvement and cost measurement processes
bring about a huge reduction in an organization’s
COQ. Error management activities can be correlated
to the three elements of COQ and the PAF model:
prevention, appraisal, and failures. Error management
training fits solidly into the prevention element.
Since error management uses data from all sources,
inputs from both appraisal and failure elements
of the PAF model provide key information for adapting,
implementing, and sustaining error management methodologies
throughout an organization.
Lack of leadership and assertiveness on the part of
individuals are the most common contributors to human
error. It is essential that organizations understand
the role leadership has on creating the right culture
where individuals feel free to speak up when things
do not seem right. In addition to creating cultures
for effective leadership and assertive team members,
high reliability organizations recognize that they
must have both proactive and reactive processes (Weick
and Sutcliffe, 2001) in place to detect, avoid, preclude,
mitigate, and preclude recurrence of errors. James
Reason’s Swiss-Cheese model graphically illustrates
how a chain of events leading up to a hazardous event
can be broken by recognizing and filling any one of
the holes in the defenses. Everyone in the organization
must consider themselves the last line of defense.
Regardless of their position or role, everyone must
be constantly looking at how to fill the holes in
technical, culture, organization, and their own individual
areas
Helen Keller said “you can’t change
the whole word; but you can change the world where
you are.” The challenge is that everyone,
regardless of their position and rank in the organization
has a responsibility to use all the information
available to be proactive in detecting, avoiding,
mitigating, and precluding recurrence of errors.
Organizations should consider the application of
error management concepts and techniques not as
a new program but as a valuable tool to compliment
and supplement their ongoing activities.
References
Committee on Quality of Health Care in American,
Institute of Medicine (2000), to err is human: building
a safer health system, Washington D.C. National
Academy of Sciences
Crosby, P.B. (1979), Quality is Free, New York:
McGraw Hill
Deming, Edward (1982), “Out of Crisis”,
Cambridge Massachusetts, Massachusetts Institute
of Technology
Feigenbaum, A.V. (1956), “Total quality control”,
Harvard Business Review, Vol.34, No.6.p.93
Gladwell, Malcom, M, (2005), Blink, New York, Little,
Brown and Company
Hart, C.A., Global Aviation Information Network
(GAIN), Presentation, Federal Aviation Administration
(undated)
Helmreich, R.L. Merritt, A.C., & Wilhelm, J.A.
(1999). “The evolution of Crew Resource Management
training in commercial aviation”, International
Journal of Aviation Psychology. 9(1), 19-32
Machowski, F. and Dale, B. G. (1978), “Quality
Costing: An examination of knowledge, attitudes
and perceptions”, Quality Management Journal,
Vol.5. No.3, p.84
Nova Public Broadcasting Series program , Why Planes
Crash,
Okray R and Lubnau, T II, (2004-2011), Crew Resource
Management for the Fire Service Tulsa Oklahoma,
PennWell Corporation
Plunkett, J.J. and Dale, B.G. (1987), “A review
of the literature on quality-related costs”,
International Journal of Quality & Reliability
Management, Vol. 4, No.1, p.40
Reason, J. (1990), Human error. New York: Cambridge
University Press
Reason J. (1997), Managing the Risk of Organizational
Accident, Aldershop, United Kingdom: Ashgate
Sandoval-Chavez, D.A. and Beruvides, M.G. (1998),
“Using opportunity costs to determine the
cost of quality: A case study in a continuous-process
industry”, Engineering Economist, Vol.43,
p.107
Schiffauerova, A. and Vince Thomson, V. Cost of
Quality: “A Survey of Models and Best Practices”,
International Journal of Quality and Reliability
Management
Weick, K. and Sutcliffe, K , (2001) “Managing
the Unexpected”, San Francisco, Jossey-Bass,
John Wiley and Sons |
 |
|
© The
Center for Error Management 2004-2011
|
|